Deep Blue Trouble
Aug 23, 2018

Our enamels come from half a dozen manufacturers around the World, most of the British ones are from the handful of manufacturers left in the area around Stoke-on-Trent, as the process shares a lot with pottery glazes and dyes, something the town was famous for. Over the last few years we’ve worked our way through hundreds of different enamels, trying to find the ones which work best for dials. Each one has different properties and these take a little time to work out, but it’s normally just a few days of refining timings/temperature/sieve gauges/copper thicknesses etc.

Earlier this year, after finalising the colours we’d launch with (which was no easy task having to whittle it down from 168 colour swatches!) we used a small vial of blue that’d been sitting in the studio for several years. It was a transparent enamel rather than an opaque, and it’d been mixed up and used by accident. Transparent enamels don’t work on copper as the metal blackens with the heat and that comes through making the dial dark and muddy. We’d experimented with them early on, with some success on precious metals, but had then focused on opaques.
This blue is an exception to that, the depth of colour was unlike anything else we'd seen. We changed the line-up and swapped it in.

It’s remarkable how much difference there is between working with one enamel and another, this particular colour caused a fair few headaches, but we hadn’t seen a translucent used in a dial like this and were determined to do it.
The first challenge we faced was the solder melting during firing. Even though temperatures and durations were the same as or less than what we'd worked with before, somehow this particular enamel dealt with the heat differently and would melt the solder holding the dial feet in place, causing the dial feet (which hold the dial onto the movement) to drop off in the kiln. Normally on the last firing, rendering the day’s work useless! This issue was solved after about three weeks. Two days after we’d worked around this the dials suddenly came out with a cloudy ring around them, almost as if the enamel had spoiled somehow. It’d been kept in a sealed container and there were no differences between these and the earlier, clear dials. This took a further fortnight to resolve. After these two problems were solved the blue remains the dial with the highest scrappage rate, taking a week to make a single one in many cases. But it is, a remarkable colour.
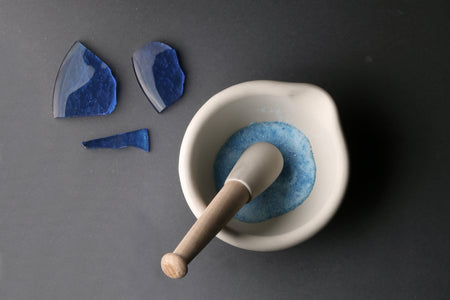
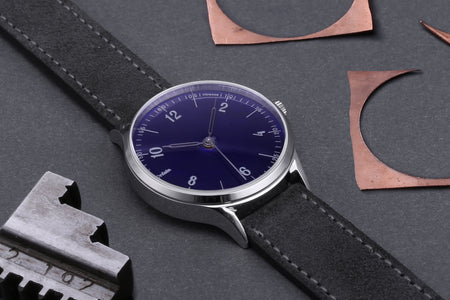
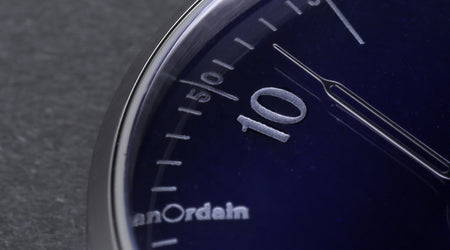
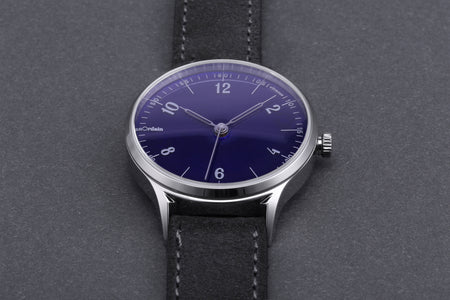