Introducing the Model 2 Porcelain: Delving Further into the Vitreous Arts
Feb 28, 2025

In the summer of 2021, our enamellers stayed in a rambling chateau outside the French city of Limoges, a place synonymous with the ‘fired arts’. It was a memorable week spent visiting the museum dedicated to the medium, the local enamel manufacturer and some great artisans working in the region. However, the city is best known for the other fired art: porcelain. Inspired by what we’d seen, and intrigued by a medium so ostensibly similar to enamel, our experiments in porcelain began shortly after returning home.
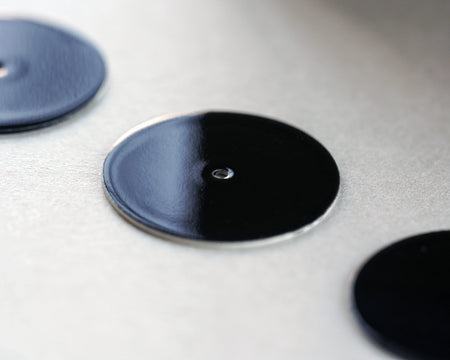
Production of the porcelain dials
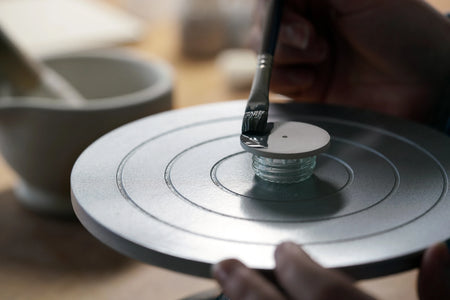
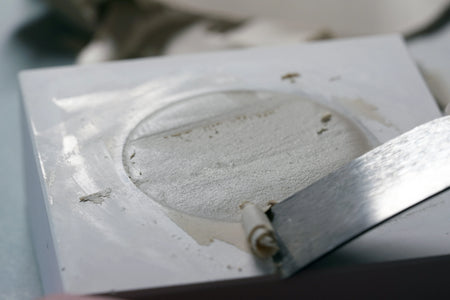
The clay dial mould
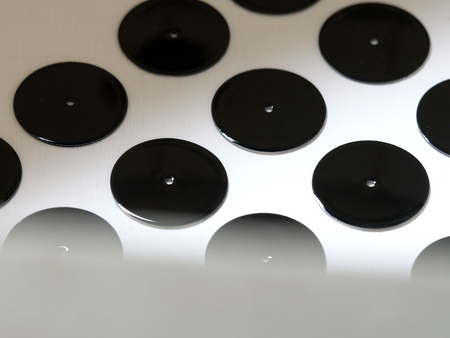
Firing dials in the kiln
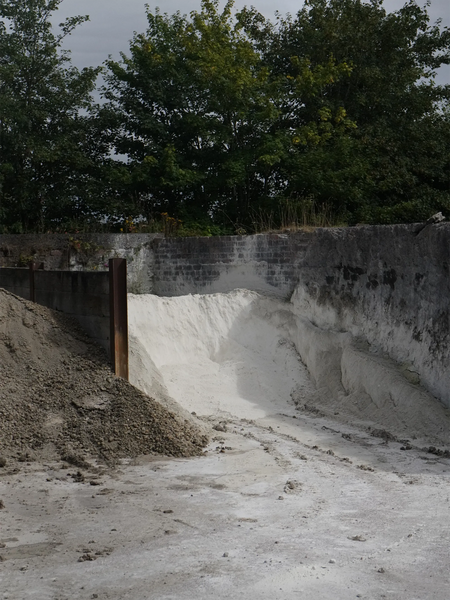
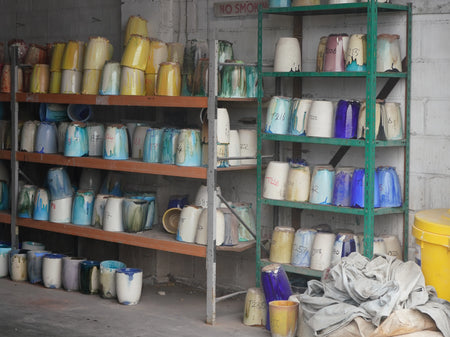
Potclays, Stoke-on-Trent
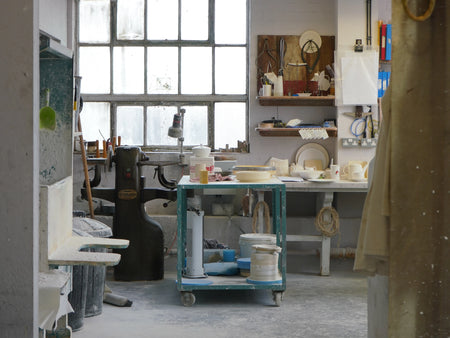
Duchess China, Stoke-on-Trent
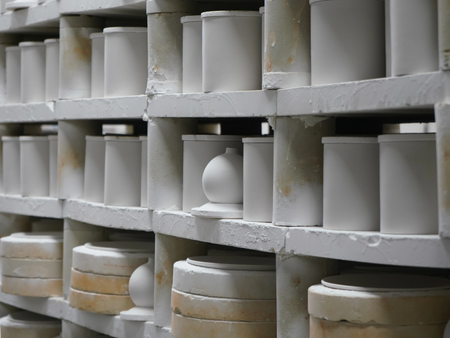
Duchess China
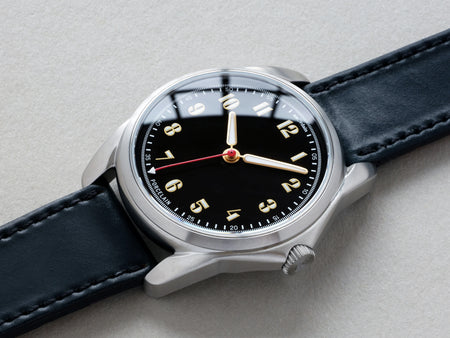
We’re currently making only the 39.5mm Model 2, but are developing the 36mm version for launch later in the year. Additionally, the porcelain dials will only be available with the G101 movement by La Joux-Perret and in the brushed case.