The Method Dial
Sep 28, 2023

After more than four years in development, we’re delighted to finally introduce the Model 3 to our core collection with the Model 3 Method.
Here at anOrdain, collaboration is central to what we do - our in-house know-how spans enamelling, metalworking, design and watchmaking. The story of the Model 3 Method incorporates all of these and more, with the addition of some high-tech light scanning, laser engraving and stamping.
But this story starts closer to home and involves another traditional craft process - woodworking. Method Studio is a renowned Scottish artisan cabinet and trunk maker founded by husband-and-wife team Callum Robinson and Marisa Giannasi. With an approach similar to our own, their work is informed and enriched by traditional processes but executed in a distinctively contemporary manner. Based in an old sawmill in woodlands outside the village of Linlithgow, near Edinburgh, Method Studio counts the likes of Hermès, Burberry and Vacheron Constantin among their clients.
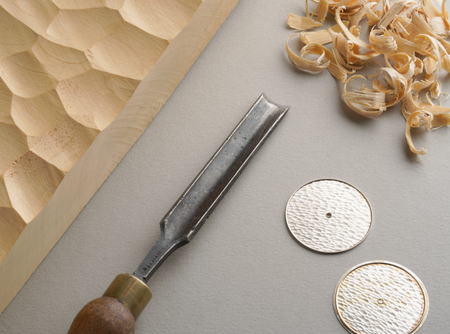
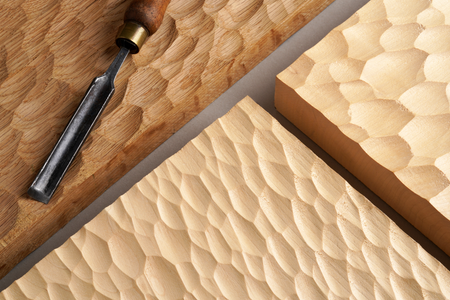
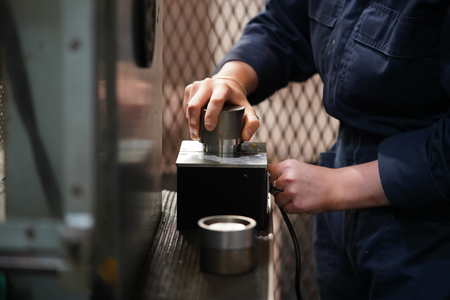
Dial stamping

Dial inspection
With the Method dial, every micro-millimetre of the dial presents different angles and depths for the enamel to fill and eventually cover, reacting to repeated firings in different ways.
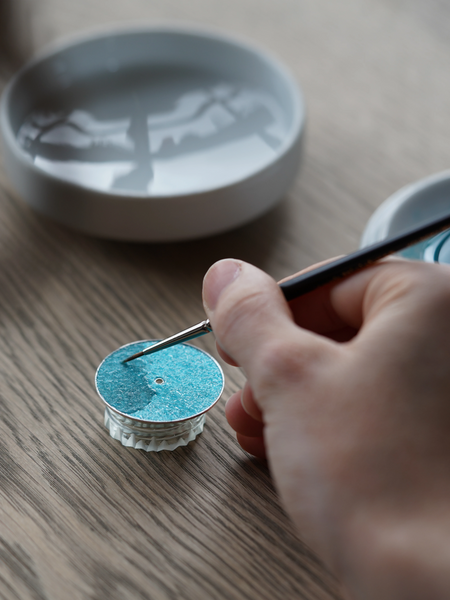
With the Method dial, every micro-millimetre of the dial presents different angles and depths for the enamel to fill and eventually cover, reacting to repeated firings in different ways.
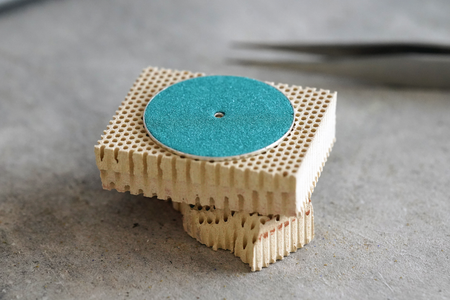
Enamelling the Method dial
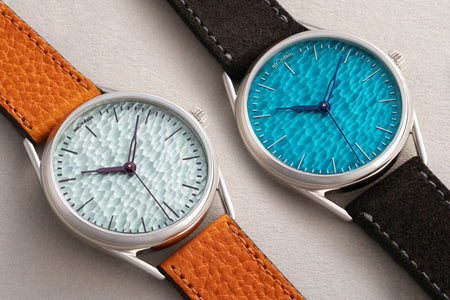
Method Lichen and Aqua
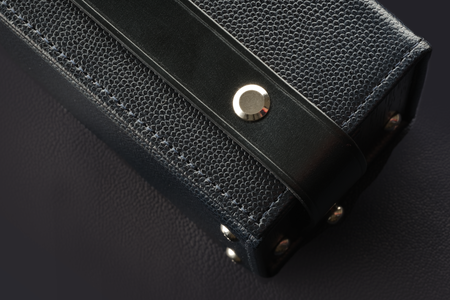
Method Limited Edition Trunk in Ebonised Oak, goatskin and bridle leather
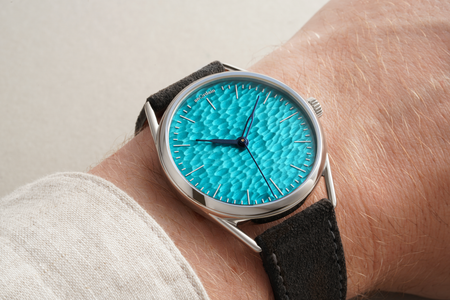
The Method Aqua on the wrist