New Studio
Jul 16, 2019

During the 10 months since the launch of Model 1 we’ve barely had time to put down our tools. To make the Model 2 possible, we’ve moved to a new purpose-built studio where we can continue to refine our processes and develop new techniques.
Our new workspace is located in the Templeton Building in the East End of Glasgow. The building was originally designed as a carpet factory for James Templeton and Son in 1892. It was turned into a business centre just under a century later and to us, this site is now home.
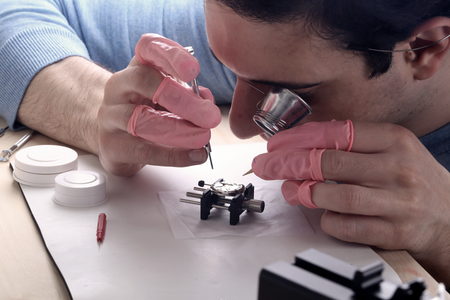
Chris working on one of our new SW210 movements.
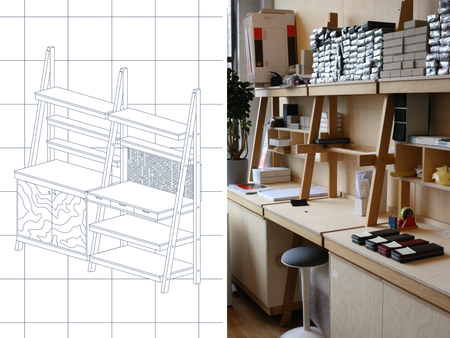
An early concept drawing of the packaging space, and the space in use.
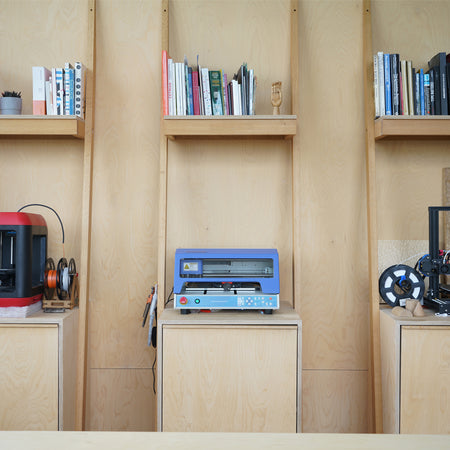
Our 3D printers and prototyping machines.
Shelving in the design room.
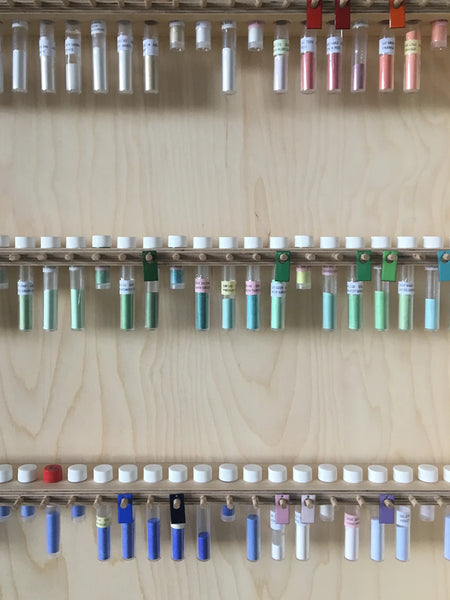
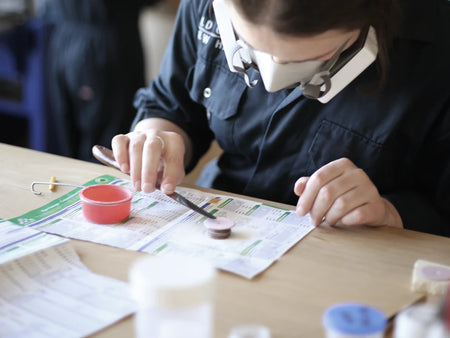
Our enamel store
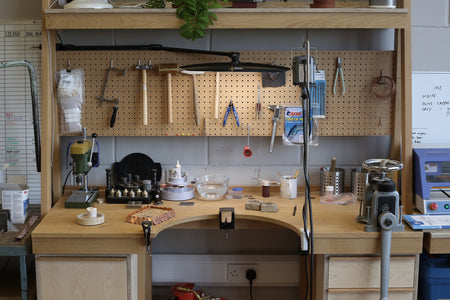
The jewellery bench.
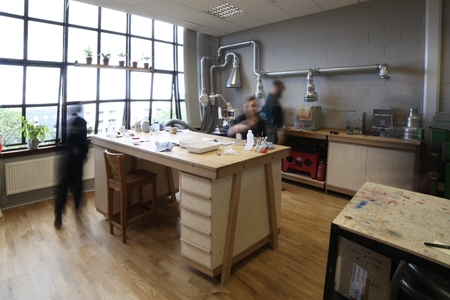
A busy day at the workshop.
One of our many young ferns.