The happy accident of the fumé dial
Oct 07, 2022

One of the pleasing things about working with vitreous enamel is its light-refractive qualities. Even the most opaque enamels have a particular vibrancy and depth of colour due to this quality. At the other end of the scale, transparent enamel gives you a vivid, jewel-like surface, which you can layer over engraved patterns that ripple through from beneath. Since we started, that’s something we’ve loved experimenting with; and as it happens, it’s an area where we’ll have some exciting new things to talk about very soon.
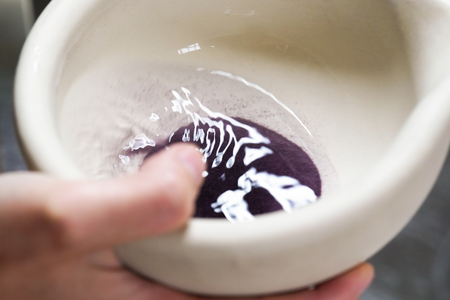
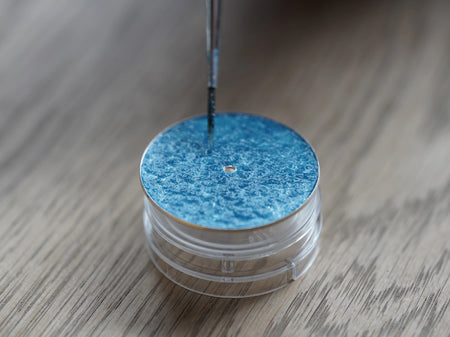
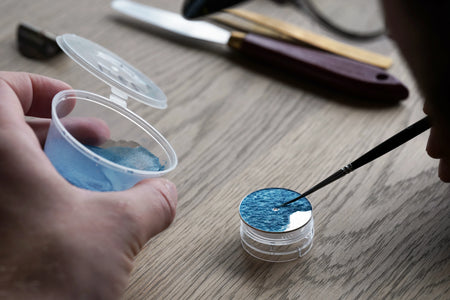
Enamelling the Blue Fumé
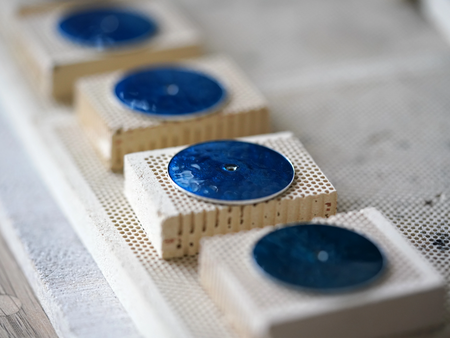
Blue Fumés post firing
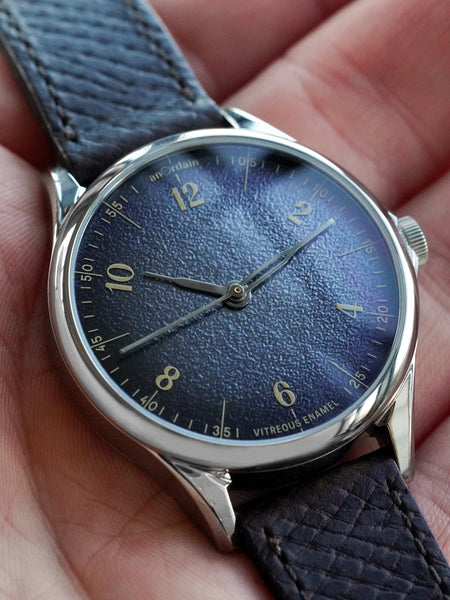
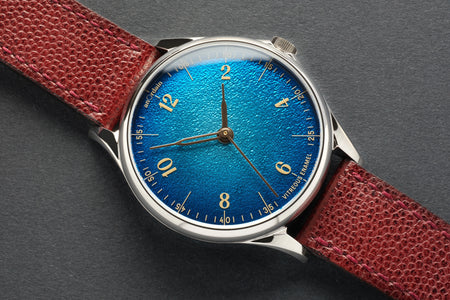
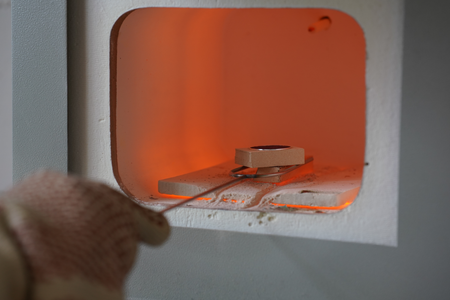
Removal from the kiln
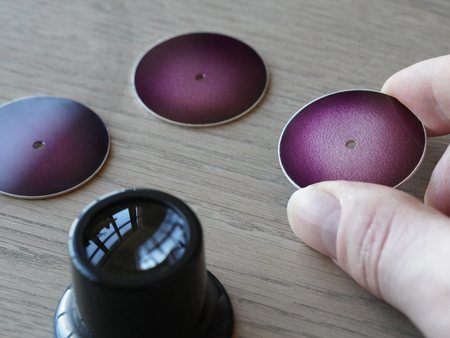
Plum Fumé dial inspection
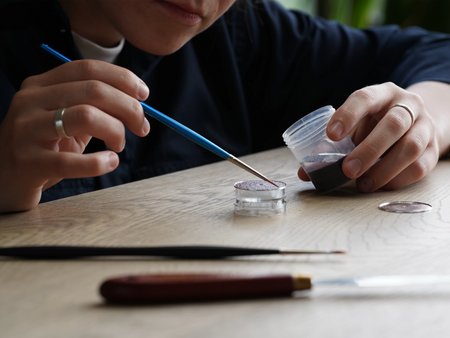
Enamelling the Plum Fumé