The Model 1 Fumé: The Development of Fumé Enamel
Dec 22, 2020

At the start of December, we launched the Model 1 Fumé: a fresh iteration of our first watch, the Model 1. Fumé enamel first appeared on our Model 2 dial in 2019, and we believe it to be the first gradated watch dial to exist in the medium of enamel. Now, the Model 1 Fumé offers a lustrous reimagining of the best-selling classic, the fumé enamel giving its dial a new and mesmerising depth. But what exactly is fumé enamel?
Fumé translates to mean 'smoked' and is the term used to describe a dial that gradates from a solid hue in the centre to a dark rim, creating a striking and dusky effect.
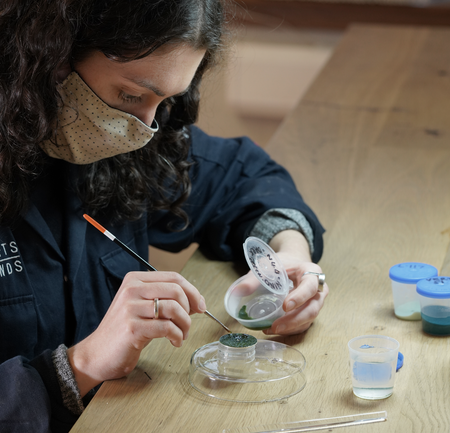
Sally at work enamelling a fumé dial